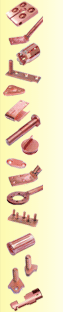 |
 |
 |
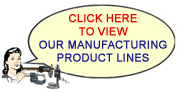 |

 |
Development &
Production of High Precision Copper components
as per Custom Design, with
Intricate Shapes & Profiles having close tolerances &
Accuracy. |
 |
 |
Expertise in Manufacturing
Engineering with subjective Knowledge of Standards,
Materials, Manufacturing Processes & Tool Making, to
produce Copper components for Electrical, High/Low Tension
Power Transmission & Electronics |
 |
 |
Expertise in 3D & 2D
Software enable us to achieve successful results. |
 |
 |
Controlling Wastage in Raw
material by Dexterously Designed Tooling &
Process Controls enable us to get optimized material
utilization. |
 |
 |
Providing Total Solution
inclusive of Post-manufacturing
Processes like Surface Finishing, Coating / Plating,
Heat Treatment & Other allied
processes like Soldering, Silver soldering, Brazing,
etc. |
 |
 |
Thorough Understanding
of Clients Design specifications &
functional requirements of the end product for Electrical &
Electronic Applications |
 |
 |
Reverse
Engineering Services & Assistance in carrying out
Design Activities / Design Up-gradation & adopting
suitable manufacturing processes to achieve Clients desired
cost effective solutions. |
 |
 |
Expertise in fault finding and
research capability, for applying corrective action.
|
 |
Copper Components
for Rotary Switches, Control Panels & Heavy Duty Current
Carrying Applications like Power Transformers, Switch gears etc.
like :
 |
CONTACTS |
 |
 |
FUSE HOLDERS |
 |
BUS BARS |
|
 |
FASTENERS / WASHERS |
 |
TERMINALS |
|
 |
CLIPS |
 |
CONNECTORS |
|
 |
SPRINGS & WIRE FORMS |
 |
RELAYS |
|
 |
COPPER PIPES & FITTINGS |
 |
COMMUTATORS |
|
 |
CUSTOM
MADE COPPER
COMPONENTS & ASSEMBLIES
AS PER CLIENTS SPECIFICATIONS |
|
ROTOR BAR |
|
|
ELECTRICAL SWITCH GEARS
&
CONTACTORS

ELECTRICAL HIGH/LOW TENSION
POWER
TRANSMISSION

AUTOMOTIVE ELECTRICALS |
MARINE ELECTRICALS

ELECTRONICS

HARDWARE & FASTENERS

REFRIGERATION &
TEMPRATURE
CONTROL |
We look at Copper from
the microscopic levels like grain homogeneity & orientation,
while manufacturing of components having extreme close
tolerances and finishes:
We are vertically
integrated with a team of various Associated ISO 9000 accredited
Manufacturing Units, each specializing in a specific field of
production Activity to ensure optimum quality with on time
deliveries:
 equipped
with CNC Turning and
Milling centers, SPMs, &
Automats like Traubs, Conventional Machines like Lathe &
Drilling, Grinding, Milling, Roll Threading Machines, Ultrasonic
Cleaning & Vibrator Deburring. Tool Room & Auxiliary
equipment facilities for Attachments & Fixtures.
 equipped
with Shearing Machines,
Power presses, Hydraulic
Power Presses, Press Brakes, CNC Turret Press, Vibrator Deburing
Machines & Fully Equipped Tool room with sophisticated
Measuring Instruments.
 equipped
with Induction Heating Facilities for small
Upset forgings,
Up-setters for head forming operations, Furnaces with Automatic
Temperature Controllers, Power Press (Pneumatic Hydraulic &
Mechanical) ,Friction Drop Hammers, Fully Equipped Die Shop &
Tool Room.
 equipped
with advanced Equipments
 We
have access
to facilites for
Specialized Heat Treatments like Nitrogen Annealing, Precipitate
Hardening, Homogenizing etc
 We
have access to facilites
for surface treatments & Plating like Chrome, Gold, Silver,
Tin, Cadmium, Chrome, Nickel / Electroless Nickel, acid washing
etc. These units have Automatic Electronic controlled equipments
to regulate plating thickness.
 includes
Shophisticated Measuring
Equipments like Surface
table, digital height gauge, Digital Precision Micrometers,
Profile Projectors, Surface finish measuring gauge, sign bars,
bench centers and all other standard Inspection Equipments.
 having
international accredition & equipped with advanced
facilities like
Computerised Spectrometer for chemical analysis, 3D Coordinate
Measuring Machines (CMM), Tensile and compressive load test
machines, NDT set up, etc.
 |
Inspection and identification
of the material at Electrolytic forming stage of Ingot to
ensure that the defective portions of the Ingots are
discarded correctly. |
 |
 |
Chemical analysis for Purity, ensuring the
composition as per required grade. |
 |
 |
Ultrasonic tests of Extrusion Bars &
Rods |
 |
 |
Checks for Work Hardening of Rolled Sheet |
 |
 |
1st piece Inspection. |
 |
 |
Patrol inspection (SPC for critical close
controlled dimensions), |
 |
 |
Final Inspection by SQC Method |
 |
 |
Checks for Work Hardening of Rolled Sheet |
 |
 |
Inspection for folds and
cracks |
 |
 |
Inspection of grain
directions of formed profiles. (1st piece for corrective
action). |
 |
 |
Testing of Ultimate
tensile/shear strengths to ensure Specifications. |
 |
 |
Microscopic Inspection of sectioned pieces
for Electric Conductive and Current Flow Tests for Joints |
 |
|
 |
|
 |
We have developed various intricate Copper items requiring
sophisticated machines for processing and have operators with
good skills. Some of the products are listed below:
|
|
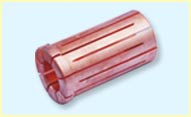 |

 |
Slender 100mm Deep Milled
slits compared to Ø 35 mm and heavy thickness of the
Wall |
 |
 |
Fine slit Milling with many inline slits,
alternate slits being in opposite directions. |
 |
|
|
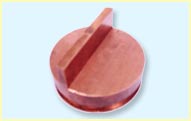 |

 |
Involves Precision Turning
and Eccentric Milling using Carbide Tipped Milling Cutters. |
 |
 |
Required constant monitoring with special
purpose dedicated gauges |
 |
|
|
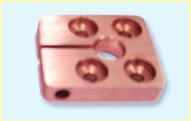 |

 |
Co-ordinate drilling required
due to precision positioning of holes |
 |
 |
Milling of the Slit done at the end of all
operations, to eliminate dimensional variations due to
springing open of the slit. |
 |
 |
Deburring the Cross hole that is
intersecting the Milled Slit required high skills. |
 |
|
|
|
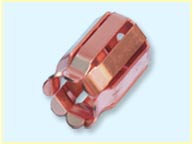 |

 |
8 Arms Contact required
development of dedicated Collapsible inserts form holder for
processing |
 |
 |
The intricate shape calls for Skills &
care to eject the component from the tool. |
 |
 |
The Operation is done on a Hydraulic
press, with variable controlled speeds, that are required at
various stages of the forming cycle. |
 |
 |
Material saving is achieved by designing
the Blanking Tool to match intricate strip lay-out
consisting interlocked fingers. |
 |
|
|
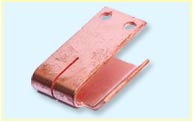 |

 |
Forming the 3 mm thick sheet
with 1.5 mm slit & Narrow U Bend of critical Inner
radius without springing back, called for a tool of unique
design |
 |
 |
Slitting was done after complete forming
to avoid distortion. |
 |
 |
Deburring of the slits was done by
Ultra-sonic cleaning, to avoid formation of inside burr. |
 |
|
|
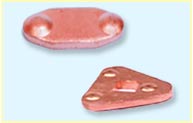 |

 |
Forming accurately Projected
Domes of exactly equal heights at the extreme edges, without
the plate bending, is a specialty in tool designing. |
 |
 |
Precision Shearing free of burrs was also
a specialty in tool design |
 |
|
|
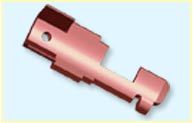 |

 |
2,5 mm Thick Main Connector
required Fine Blanking Tools & specialized Process. |
 |
 |
Critical Bending of the Notched End
required extra care & presicion |
 |
 |
Pressure spin riveting for Joining the
thin Copper Lug to the thick Thick Main Connector to ensure
solid joint without any air gap. |
 |
|
|
|
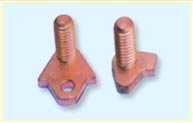 |

 |
Forged Contact, with large
eccentric upset wherein 7mm Ø bar is Spread to 452 sq
mm at 25mm eccentricity. |
 |
 |
By our know-how we innovated a unique
process to achieve minimum waste, thus maximum cost saving.
Forming this profile by conventional Head Forging would
result in huge copper wastage due to large one sided Flanged
Head. |
 |
|
|
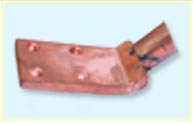 |

 |
Flat bar forged to form flat
tang of 8mm thickness with Forged bend to required angle. |
 |
 |
Complex milling fixtures were made to
ensure high precision squareness and flatness at the desired
angle with respect to the rod |
 |
|
|
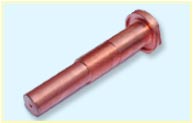 |

 |
1.25 bar upsetted to
2.5 Ø x 3/8 thick flattened top. |
 |
 |
Then precision Machined to achieve various
Diameter on the Bolt Stem. |
 |
|
|
|
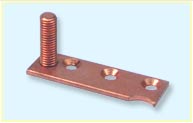 |

 |
Silver soldering of 3/8
UNC studs into 3mm thick copper Bus bars. |
 |
 |
Capillary action of the silver solder
through the entire thread length maintained to achieve
Sturdy Joint while ensuring Perfect Conductivity. |
 |
|
|
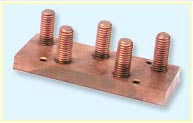 |

 |
Silver soldering of 3/8
UNC studs into Tapped Holes of the 6 and 10mm thick copper
Bus bars. |
 |
 |
Capillary action of the silver solder
through the entire thread lengths maintained to achieve
Sturdy Joint while ensuring Perfect Conductivity (To Carry
400 & 800 amps capacity) |
 |
|
|
|
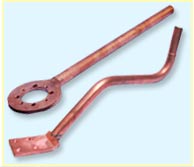 |

 |
Large & Thick
Copper Flats are precision machined to flatness, parallelism
and thickness within 0.02mm T.I.R |
 |
 |
Silver brazing the tang into a
rod involving complex fixturing to ensure that: |
 |
|
 |
Alignment is within 0.05mm T.I.R. |
 |
|
 |
The brazing through capillary action
covers the whole joint area giving strength and excellent
conductivity. (Being conductors for very heavy current
flows) |
 |
 |
Co-ordinate drilling after
brazing to ensure accuracies |
 |
|
|
|
|